Fuel
delivery systems have one common element that is at the
center of every type of module assembly or in the tank
hanger and that is the electric fuel pump. All electric fuel
pumps operate on current from the vehicles battery or
charging system to move fuel, under specific pressure to the
carburetor or fuel injectors. There are three basic electric
fuel pump types:
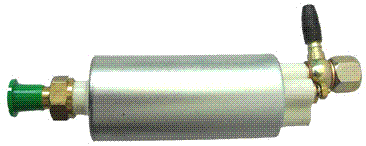
Turbine:
An
armature located inside the fuel pump case operates a
turbine blade, which turns at high speed to create and
maintain the pressure needed to function correctly. The fuel
is skimmed from the spinning blade and directed into the
outlet of the pump. These turbine type pumps are typically
used on multi-port fuel injected vehicles. Although the
operating pressures of this type of pump are similar to
other styles, closer tolerances make it sensitive to fuel
contamination such as foreign particles and other outside
influences.
Gerotor:
As
the name indicates, the gerator is a gear drive pump, which
also uses an armature to drive a smaller gear that in turn
drives a larger outer gear. Because of the precise gearing,
gerator style pumps are quieter when operating. The rotation
of the gear creates both vacuum drawing fuel into the pump
and a contraction that forces fuel out of the pump. This
type of pump is also used on multi-port fuel injected
vehicle such as ones used by Ford and Chrysler. Similar to
the turbine design, gerator type pumps are sensitive to fuel
contamination.
Rollervane:
While
all of the stated types of pumps use an armature, the roller
vane pump drive metal rollers that are fitted to a rotor. A
vacuum is created by the rollers that pull fuel into the
pump while the driven rollers also force the fuel from the
pump chamber under pressure. These types of pumps can
tolerate more fuel contaminates, but the trade off is that
they are noisier than the turbine and gerator type pumps.
You will find rollervane pumps also used in multi-port fuel
injected applications.
Typical
Module Designs
Most vehicle manufacturers use in
the tank module assemblies, which are made of fuel resistant
plastic. Autobest Module Assemblies are built under strict
guidelines to meet or exceed manufacturers’ requirements.
Because we are an O.E.M. supplier, we realize that the
quality in raw materials and design results in higher
performance and durability.
What makes up a Module Assembly?
Ø
The
Reservoir – A
plastic molded fuel-resistant body. It holds gasoline to
ensure
that
there is fuel available during all operating conditions.
Think of it as a tank
within
the gas tank.
Ø
The
Strainer –
A filter located outside the module assembly ensures that
the
gasoline
inside the module has been filtered or “strained” prior
to being delivered
to
the engine. Some applications have two strainers one outside
and one on the
inside
of the module. The strainer on the inside is not a
serviceable component of
the
module assembly.
Ø
The
Fuel Pump –
The electrical component that operates by sending fuel under
pressure
to the engine.
Ø
The
Float –
A component that is attached to measuring device that
indicates the
fuel
level in the tank.
Ø
The
Sender Unit
– Works with the float and controls the fuel gauge inside
the vehicle.
Ø
The
Spring –Expands
inside the gas tank based on operating temperatures keeping
the reservoir at the bottom of the tank.
The fuel pump creates pressure
within the fuel lines to ensure that there is a constant
flow and no interruption of fuel to the fuel injectors or
carburetor. Because of varying driving conditions such as
area that are dusty or prone to severe conditions, strainers
are part of the module assembly. Even to best strainer
cannot keep all particles out of the fuel system but, not
having one gives virtually no protection from foreign
particles of be ingested by the gasoline engine.
Typical
Hanger Designs
The
design of fuel pump Hangers shares some of the same
characteristics of the module assemblies. Although Hangers
are more simplistic in comparison, they operate to serve the
same basic function.
What
makes up the Hanger Assembly?
Ø
The
Metal Hanger – The
base that holds and secures the other component
securely.
It is mounted at the fuel tank either at the top or on the
side depending
on
the application.
Ø
The
Fuel Pump –
Is mounted to the metal Hanger to which the inside the tank
fuel
lines are attached at one side and the strainer is at the
other side.
Ø
The
Reservoir –
Keeps an ample supply of fuel and located below the fuel
pump
assembly. As in the module design, ensuring that there is a
constant
supply
of gasoline available in low fuel conditions and during
sharp turns is the
primary
purpose of this design.
Ø
The
Strainer –
The filter, which “strains” the fuel prior to being
drawn into the fuel pump assembly.
As with the Module Assembly,
strainers are an essential component of the Hanger Assembly
and should always be replaced when installing the hanger.
Failure to do so will void the warranty on the Hanger
Assembly. This simple practice will save time and
aggravation down the road.
|